Industrial automation is the use of robotics and software to enable autonomous systems to control equipment and procedures used in a variety of industries.
Industries use automation to boost output, lower labour costs, employee benefits costs, and other related costs while improving precision and flexibility.
Mechanism Behind Industrial Automation :
Mechanization, which was a result of the Industrial Revolution, led to the production of cheaper and more plentiful commodities.
In general, mechanical processes in industries produced things more quickly and in larger quantities, but they still needed experienced personnel. Machines needed operators, and when mistakes were made, they wasted supplies, interfered with production, and even broke things.
Controlling Systems :
Control loops were added to machine functioning with the advent of automation. These can be fully automated closed loops or open control loops that accept input from humans.
Locally and remotely located monitoring and control are possible with industrial control systems (ICS). Industries are able to function around the clock because to these increasingly sophisticated control methods.
Advancements :
The quality has improved, errors have decreased, and productivity has grown. Automation does, however, have significant drawbacks, such as expensive startup costs, decreased employment of workers, and the removal of some morally upstanding human control.
These occurrences may rise as automation develops more and becomes more common in emerging industries.
Let’s dive a little deeper in industrial automation!
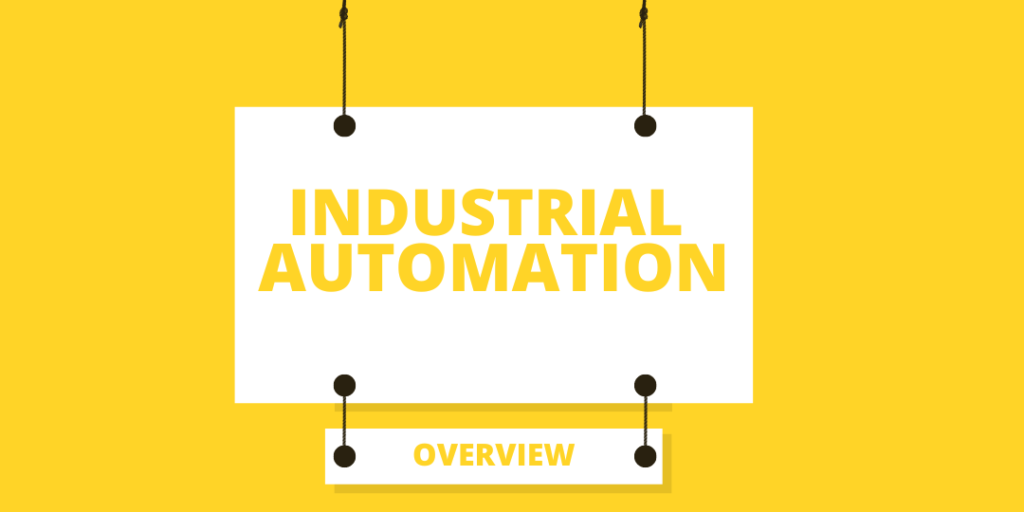
History
Since the British industrial revolution, a lot of work has gone into creating sophisticated systems that can assist workers with a variety of production-related jobs.
A combination of raw materials are processed through a number of machinery in an industrial manufacturing process to create the finished good.
The term “machine” in this context can refer to either electromechanical devices, such as a motor, drill, conveyor belt, etc., or chemical machines, such as dryers, ovens, chemical combustion systems, etc.
It is now quite impossible to envisage a production line without automation systems because industrial automation has completely taken over the production process in industries.
Implementing automation systems in industrial production is influenced by a number of issues, including the need for high-quality products, high standards for product dependability, high production volumes, etc.
Industrial Automation: What Is It?
Industrial automation is the practise of using mechanised technology to operate machines and other industrial equipment while minimising human involvement in decision-making and manual command processes.
Although the aforementioned definition is undoubtedly complicated, let’s try to comprehend what industrial automation is with the aid of a little example.
An Illustration Of Industrial Automation
Think about a manual industrial production process where a worker is monitoring the oven’s temperature. Assume the objective is to raise the temperature and keep it there for around 30 minutes.
In order to raise the temperature to the required level, the operator must first adjust the fuel supplied to the oven by operating a valve.
Once the required temperature has been reached, it must be maintained for the following 30 minutes by continuously regulating the valve, i.e., increasing or decreasing the fuel based on the temperature.
Thanks to industrial automation, the entire process is now handled without an operator’s assistance. The temperature is first reported to a computer by a temperature sensor that is situated close to the oven.
The fuel supply to the oven is now managed by a motorised valve that is also computer controlled. The computer will open the valve to allow more gasoline initially based on the temperature data from the sensor. The valve is shut off once the desired temperature has been reached.
However, based on the temperature readings, the computer can open or close the valve, even to enable the least quantity of fuel to flow. Once the allotted 30 minutes have elapsed, the computer’s timer will signal that it is time to shut down the system completely.
Conclusion :
The aforementioned illustration might seem ambiguous, yet it aids in understanding how a typical industrial automation system might be put into practise. The task in the aforementioned example is entirely completed by the automation system with zero human involvement.
ALSO READ
You may also like our other related articles on automation :